Wide Range of Consumables and Equipment - Ferrous Foundry
Filtration
The primary function of the gating system is to introduce metal quickly into the mould without turbulence and to prevent non-metallic inclusions in the liquid metal from entering the casting. While this is still their main function, they are also used to simplify running systems allowing more castings to be made in a mould and improving the yield of castings.
Foseco offers a range of carbon bonded alumina, silicon carbide, zirconia and graphite based filters for steel, iron and non ferrous alloys.
The variety of steel filtration systems available facilitate the production of steel castings with improved integrity, physical properties, and surface finish. Production costs are reduced particularly through the reduction of scrap and post casting upgrading.
Filters very efficiently remove particulate non metallic inclusions and liquid slag form the molten metal stream before mould filling. The casting producer can achieve reduced scrap and improved yields. The variety of iron alloys cast have different requirements so a range of filter efficiencies and pore sizes are available.
SEDEX is a range of silicon carbide based ceramic foam filters designed for use in grey and ductile iron applications to provide a smooth laminar flow of molten metal and prevent the ingress of slag, magnesium reaction products, inoculant residues or sand grains into the mould cavity. The high filtration efficiencies combined with a reduction in turbulence often allows gating systems to be greatly simplified. SEDEX filters can be positioned vertically, horizontally, or diagonally in a suitably designed runner system.
SUPER SEDEX is a range of new generation silicon carbide based ceramic foam filters with a consistent, high level performance in terms of metal flow rate and filtration efficiency. The consistent pouring times and enhanced flow rate characteristics make SUPER SEDEX ideally suited for vertically parted moulding applications such as DISAMATIC. The improved open pore ceramic structure of SUPER SEDEX allows foundries to:
> Use finer porosity for higher filtration efficiency
> Maintain uniform pouring times
> Achieve improved metal flow rates
STELEX PrO is a range of carbon aluminium oxide ceramic foam filters and are particularly suited to the production of white iron and large ductile iron castings. Previously, it has not been possible to filter these castings due to problems with chill, filter capacity and filter strength. Practical experience has shown the benefits of filter-clean castings and, more specifically, improvements in surface finish leading to significant savings in fettling and cleaning operations.
SEDEX is a range of silicon carbide based ceramic foam filters designed for use in grey and ductile iron applications to provide a smooth laminar flow of molten metal and prevent the ingress of slag, magnesium reaction products, inoculant residues or sand grains into the mould cavity. The high filtration efficiencies combined with a reduction in turbulence often allows gating systems to be greatly simplified. SEDEX filters can be positioned vertically, horizontally, or diagonally in a suitably designed runner system.
SUPER SEDEX is a range of new generation silicon carbide based ceramic foam filters with a consistent, high level performance in terms of metal flow rate and filtration efficiency. The consistent pouring times and enhanced flow rate characteristics make SUPER SEDEX ideally suited for vertically parted moulding applications such as DISAMATIC. The improved open pore ceramic structure of SUPER SEDEX allows foundries to:
> Use finer porosity for higher filtration efficiency
> Maintain uniform pouring times
> Achieve improved metal flow rates
STELEX PrO is a range of carbon aluminium oxide ceramic foam filters and are particularly suited to the production of white iron and large ductile iron castings. Previously, it has not been possible to filter these castings due to problems with chill, filter capacity and filter strength. Practical experience has shown the benefits of filter-clean castings and, more specifically, improvements in surface finish leading to significant savings in fettling and cleaning operations.
Round filters are more commonly used in KALPUR direct pour applications where they are located inside an insulating or exothermic feeder sleeve, with optimum feed characteristics being achieved when the filter is allowed to float after pouring
SEDEX - Ceramic foam filter for filtration of iron, copper & copper-based alloy castings
STELEX PrO - Carbon bonded ceramic foam filters for the production of all grades of steel & iron castings (patented)
STELEX ZR - Zirconia based ceramic foam filters for the production of steel & iron castings
SIVEX FC - Foam filter for liquid aluminum alloys
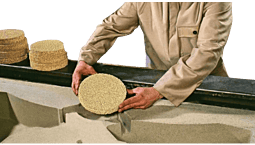
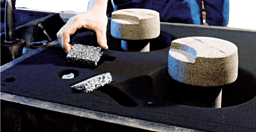



